Zero-emission waste heat provides warmth to thousands of district heating homes
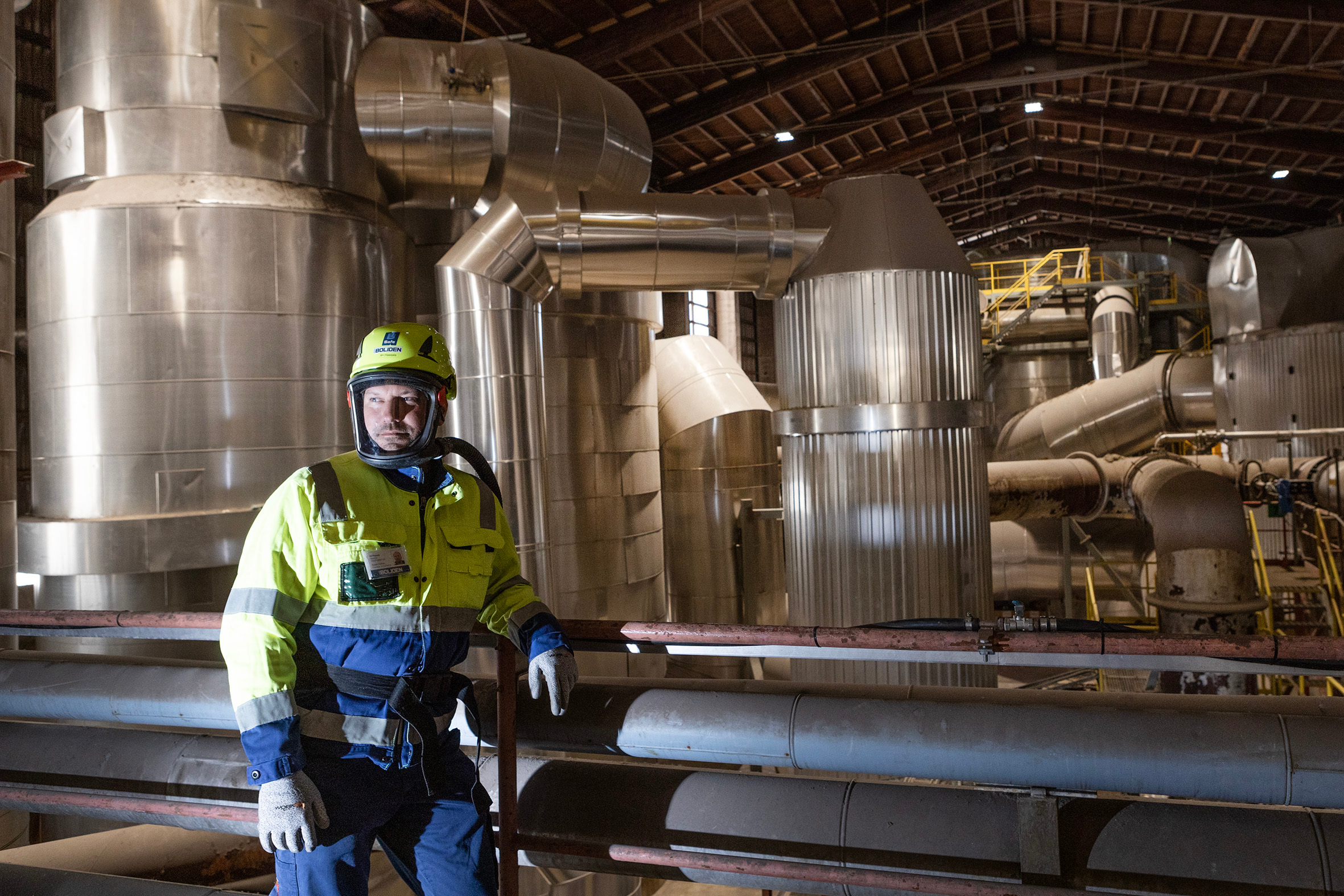
More than 40% of the district heat produced by Kokkolan Energia is produced from waste heat generated in Boliden’s processes. In the summer months, waste heat covers practically the entire district heating need of Kokkola, so that the emission-free heat generated as a by-product of zinc production alone is enough to heat the homes and domestic water of more than 35,000 Kokkola residents.
Kokkola Industrial Park has been designed, already during its construction phase, so that operators in the area can utilise the products created in each other’s processes.
“The area is a good example of circular economy even before the word circular economy was used,” says Aki Haasala, Boliden’s Energy Efficiency Manager.
The chain of utilising the circular economy also extends to the homes of district heating residents in Kokkola, as heat generated in the production processes of Boliden’s factories is directed to Kokkolan Energia’s district heating network. Aki Haasala explains the production process, the by-product of which is the heating of thousands of homes in the Kokkola region.
Where is waste heat generated and how is it recovered?
In Boliden’s zinc manufacturing process, waste heat is generated in two stages, in roasting and as a by-product of the cooling process at the sulphuric acid plant.
In the roasting phase, zinc concentrate burns in two boilers at temperatures above 900 degrees. In roasting, sulphur is burned out of the concentrate, which produces roasting material used in zinc production, and sulphur dioxide gas, heat and steam as by-products.
Roasting takes place in the furnace with high heat and air. The two boilers are fed with a total of approximately 52–57 thousand kilograms of concentrate per hour. Sulphur burns spontaneously in the furnace, so only air is needed for fuel. The fuel gases form sulphur dioxide, which is transferred to a sulphuric acid plant for processing. The roast goes to the zinc plant’s cleaning facility, where it is used to produce a zinc solution.
In the roasting boiler process, heat is recovered with feed water from Kokkolan Energia’s power plant. The water goes back to the power plant as steam with a temperature of 280 degrees, after which the heat obtained from it is first utilised at the power plant before it leaves for the district heating network at 65–115 degrees, adjusting according to the outside temperature.
The heat generated in Boliden’s Kokkola process has been recovered and utilised as district heat for decades, ever since the zinc plant started its operations. Without waste heat recovery, the heat generated in the cooling process would be driven into the sea and a large amount of energy would remain unused.
The sulphuric acid plant has potential to increase waste heat recovery
Most of the waste heat utilised in district heat production comes from the roasting process, but waste heat is also recovered from Boliden’s sulphuric acid plant.
“There is more potential for producing waste heat, for example, at the sulphuric acid plant,” says Aki Haasala.
At the sulphuric acid plant, water is mixed with sulphur dioxide gas, and the process begins to heat up in an exothermic reaction. The temperature is adjusted to suit the process according to the running situation of the process. The intermediate circulation water cools the sulphuric acid, and the hot water moves forward to heat the district heating network with the help of the city’s heat exchangers.
Cooperation to develop waste heat recovery
According to Aki Haasala, there is a huge amount of potential in utilising industrial waste heat.
“If all the waste heat generated in the KIP area could be utilised, there would certainly be no need to use fossil fuels, and wood burning in energy production could also be significantly reduced,” Haasala believes.
Boliden aims to be the world’s most climate-friendly and valued producer of metals. For the Kokkola zinc plant, achieving climate targets means concrete measures to improve energy efficiency and reduce carbon dioxide emissions. The utilisation of waste heat is continuously investigated in order to identify potential sites.
“There’s a lot of interest in utilising waste heat more extensively and finding new sites, because we want to continuously develop our operations in this area as well,” Haasala says.
Boliden has also conducted studies related to the utilisation of waste heat with Centria and Motiva. Cooperation with Kokkolan Energia will be deepened, because there is still a lot of potential, and good cooperation will develop the district heating network of the factory area to meet future needs.